In the ever-evolving landscape of industrial automation, a revolutionary concept has emerged, transforming the traditional narrative of robots replacing humans. Collaborative robots, or “cobots,” represent a paradigm shift in how we think about human-robot interaction. These sophisticated machines, unlike their predecessors, are designed to work alongside humans in shared spaces, creating a symbiotic relationship that enhances productivity while maintaining workplace safety.
The dawn of collaborative robotics marked a pivotal moment in manufacturing history. While conventional industrial robots remained confined behind protective barriers, cobots broke free from these constraints, introducing a new era of human-machine cooperation. These remarkable devices, equipped with advanced sensors and adaptive programming, can detect human presence and adjust their behavior accordingly – a technological leap that seemed like science fiction merely a decade ago.
The Technical Marvel Behind Cobots
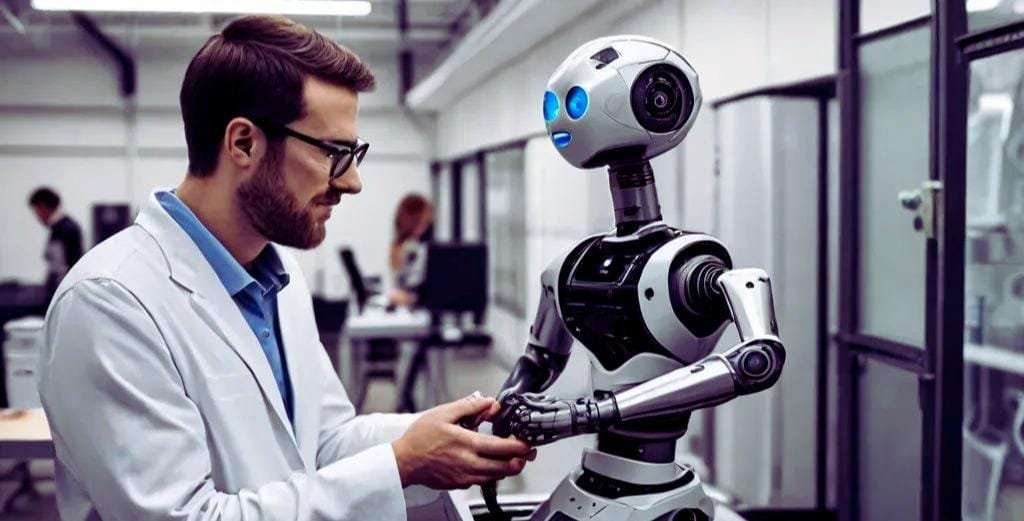
At the heart of cobot technology lies an intricate network of sensors, sophisticated algorithms, and cutting-edge safety features. Force-torque sensors enable these machines to detect the slightest unexpected contact, triggering immediate stops to prevent accidents. This inherent safety mechanism, combined with rounded edges and lightweight materials, makes cobots fundamentally different from their industrial counterparts.
Perhaps most intriguing is the neural network architecture that powers modern cobots. These artificial neural networks, inspired by the human brain’s structure, enable cobots to learn from experience and adapt to changing circumstances. Through demonstrations and intuitive programming interfaces, workers can “teach” these machines new tasks without requiring extensive coding knowledge. This democratization of robotics has opened doors for small and medium-sized enterprises that previously found automation out of reach.
Real-World Applications and Industry Impact
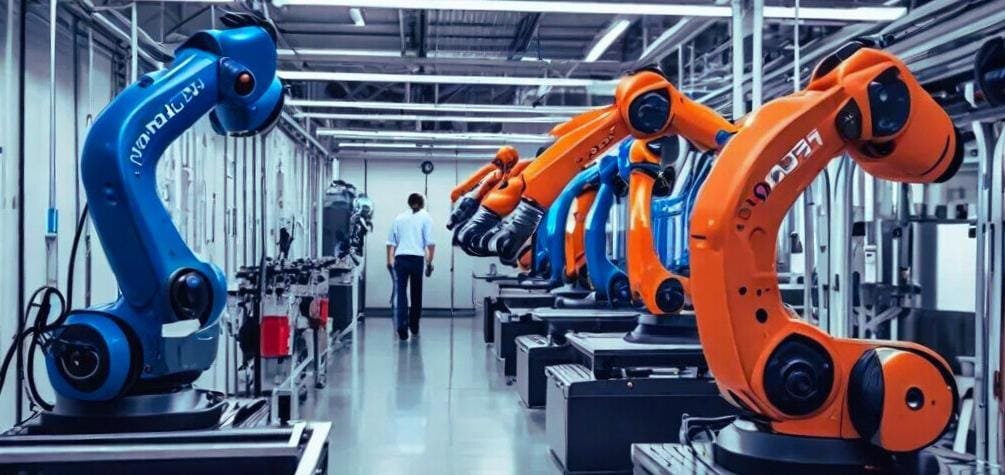
The versatility of cobots has led to their adoption across diverse industries, revolutionizing traditional workflows in unexpected ways. In automotive assembly lines, they work hand-in-hand with humans, handling repetitive tasks while workers focus on quality control and complex assembly procedures. Medical facilities employ cobots for precise laboratory work, where consistency and accuracy are paramount. Even small-scale electronics manufacturers have embraced these collaborative partners for intricate component placement.
Consider the remarkable case of a Danish furniture manufacturer who integrated cobots into their production line. Within months, they reported a 50% increase in productivity while maintaining their entire workforce – the cobots complemented human skills rather than replacing them. This success story isn’t unique; across industries, companies are discovering the transformative potential of human-robot collaboration.
Economic and Social Impact
The integration of cobots into the workforce has sparked fascinating economic ripples that extend far beyond the factory floor. Initial concerns about job displacement have given way to a more nuanced understanding of human-robot collaboration. Studies show that companies implementing cobots often create new roles focused on robot operation and maintenance, while existing employees upgrade their skills to handle more complex tasks.
Yet, the journey hasn’t been without challenges. The learning curve associated with cobot implementation can be steep, and organizations must invest in comprehensive training programs. However, the return on investment often justifies these initial hurdles, with many businesses reporting significant improvements in both productivity and worker satisfaction.
Psychological Aspects of Human-Robot Collaboration

One often overlooked aspect of cobot integration is its psychological impact on human workers. Research has shown that properly implemented collaborative robotics can actually increase job satisfaction and reduce workplace stress. Workers report feeling empowered rather than threatened when cobots take over repetitive, physically demanding tasks, allowing them to focus on more engaging aspects of their work.
Environmental Considerations
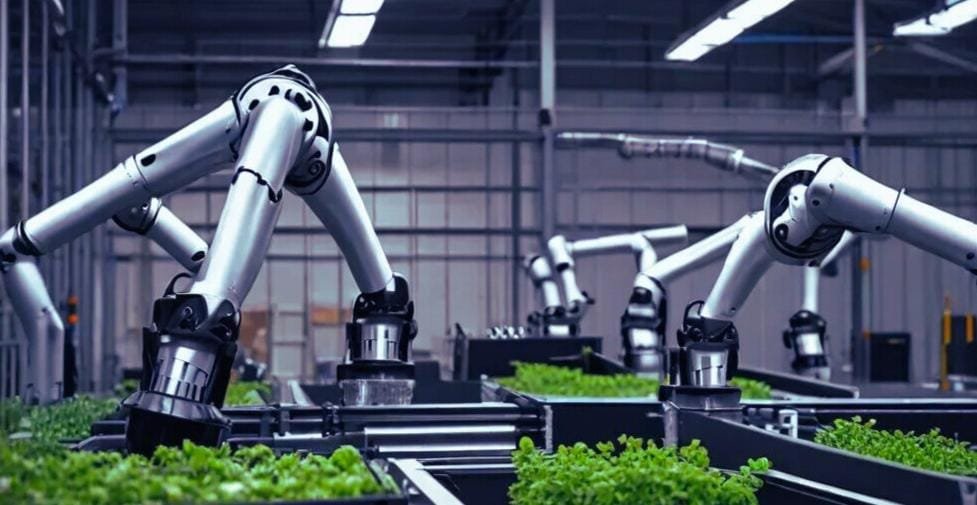
In an era of increasing environmental consciousness, cobots are proving to be unexpected allies in the fight against climate change. Their precise operation results in less waste, reduced energy consumption, and more efficient use of resources. Some manufacturers have reported up to 30% reduction in material waste after implementing cobot-assisted processes.
The Future Landscape
As we peer into the future of human-robot collaboration, the possibilities seem boundless. Advances in artificial intelligence and machine learning are pushing the boundaries of what cobots can achieve. Imagine cobots that can anticipate human actions, adapt to changing environments in real-time, and even learn from their mistakes – these capabilities are already emerging in research laboratories worldwide.
Conclusion
The evolution of cobots represents more than just technological advancement; it symbolizes a fundamental shift in how we approach automation. By bridging the gap between human creativity and robotic precision, cobots are paving the way for a future where humans and machines work together seamlessly, each leveraging their unique strengths. As this technology continues to mature, we can expect even more innovative applications that will further reshape the workplace of tomorrow.
Frequently Asked Questions (FAQ)
Q: Are cobots safe to work with?
A: Absolutely. Cobots are engineered with multiple redundant safety systems, including force-limited joints, sophisticated proximity sensors, and advanced collision detection algorithms. These safety features are continuously monitored and updated in real-time, making cobots extremely safe for human interaction. Unlike traditional industrial robots, cobots can detect abnormal forces as small as a few newtons and respond within milliseconds to prevent any potential harm.
Q: How much training is required to operate a cobot?
A: The training requirements vary depending on the complexity of the intended applications. Basic operation and simple programming can typically be learned in 2-5 days. However, for more advanced applications involving complex motion sequences or multiple tool changes, training might extend to 2-3 weeks. Many manufacturers offer comprehensive training programs, including hands-on workshops and online learning modules. Additionally, most cobots feature intuitive teach pendant interfaces and can be programmed through physical demonstration, significantly reducing the learning curve.
Q: What’s the typical return on investment (ROI) for implementing cobots?
A: ROI calculations for cobot implementation are multifaceted and depend on several factors. While initial investment costs range from $20,000 to $100,000, many companies report breaking even within 12-18 months. Factors affecting ROI include application complexity, production volume, existing process efficiency, and labor costs. Beyond direct financial returns, companies often see additional benefits such as improved product quality, reduced waste, and increased workplace safety, which contribute to the overall value proposition.
Q: Can cobots completely replace human workers?
A: No, cobots are specifically designed to complement human workers, not replace them. They excel at repetitive, precise tasks but lack the adaptability, critical thinking, and problem-solving abilities that humans possess. Instead of replacement, cobot implementation typically leads to role evolution, where workers transition to higher-value tasks involving oversight, quality control, and process optimization. This collaboration between humans and cobots often results in increased overall productivity and job satisfaction.
Q: What industries can benefit from cobot implementation?
A: The applications for cobots span across numerous industries, each finding unique ways to leverage this technology. Manufacturing sectors, including automotive, electronics, and consumer goods, have been early adopters. Healthcare facilities use cobots for laboratory automation and medical device assembly. The food and beverage industry employs cobots for packaging and quality control. Even traditionally labor-intensive industries like agriculture and construction are discovering innovative applications for collaborative robotics. Any industry requiring precise, repetitive tasks while maintaining human oversight could potentially benefit from cobot integration.
Q: What maintenance requirements do cobots have?
A: Cobots are designed for minimal maintenance compared to traditional industrial robots. Typical maintenance includes regular software updates, periodic calibration checks (usually every 6-12 months), and occasional replacement of wear parts like gripper pads or sensors. Most cobots feature self-diagnostic capabilities that can alert operators to potential issues before they become problems. Manufacturers generally recommend annual preventive maintenance inspections by certified technicians.
Q: How do cobots impact workplace culture?
A: The introduction of cobots often leads to positive changes in workplace culture. Studies have shown increased employee engagement as workers transition from repetitive tasks to more skilled roles. Companies report improved team dynamics as cobots handle monotonous work, allowing humans to focus on creative problem-solving and process improvement. However, successful integration requires clear communication, proper training, and management support to address any initial concerns or resistance to change.
Q: What are the latest developments in cobot technology?
A: Recent advances in cobot technology include enhanced AI capabilities for better human interaction, improved force sensing for more delicate tasks, and advanced vision systems for greater environmental awareness. New developments in end-effector technology are expanding application possibilities, while improved programming interfaces are making cobots even more accessible to non-technical users. Research is ongoing in areas such as natural language processing for voice commands and predictive movement algorithms for smoother human-robot collaboration.
Q: How do cobots compare to traditional industrial robots in terms of cost and flexibility?
A: Cobots generally have lower total cost of ownership compared to traditional industrial robots. They require minimal safety infrastructure, are easier to program and redeploy, and often have lower maintenance costs. While they may not match the speed and payload capacity of traditional robots, cobots offer superior flexibility and can be quickly reprogrammed for different tasks. This makes them particularly attractive for small and medium-sized enterprises or companies with varying production requirements.
Q: What safety standards govern cobot operations?
A: Cobot operations are governed by several international safety standards, including ISO/TS 15066 (specifically for collaborative robots), ISO 10218-1, and ISO 10218-2. These standards define safety requirements for industrial robots and robot systems, including specific provisions for collaborative operations. Compliance with these standards is mandatory in most jurisdictions, and manufacturers must ensure their cobot installations meet all relevant safety requirements through risk assessment and appropriate implementation measures.